ESD Matting
To eliminate electrical build up, start from the ground up. Anti-Static bench & Floor matting, cut to your requirements or available in bulk rolls.
Electrostatic discharges (ESDs) can generate stray sparks that can cause irreversible damage to static sensitive components such as printed circuit boards. Several methods are available to prevent static electricity from damaging your electronic components. To eliminate electrical build-up, it is a good idea to start from the ground up with ESD mats, the core assets of an ESD Control Plan.
What are ESD Mats?
Simple ESD mats are typically a integral part of the ESD workstation, particularly in areas where hand assembly occurs. It is important that each bench, or work surface, is covered with the proper ESD material and that the mat is grounded using metal grounding hardware snaps and ground cords connecting the work-surface mat to the common point ground. Without this grounding, the mat would protect the item being worked on initially, but it would then transfer the ESD to the following item, the person holding it, or even back to the item it was originally intended to protect.
Walking alone can create static electricity and ESD matting can help to disperse this electricity through electrically conductive carbon fibres woven throughout. Consequently, the ESD flows at a slower rate across the surface of the mat which in turn neutralises it. There is also matting available which is appropriate to use on workbenches, trolleys and other surfaces.
ESD Bench and Floor Matting is available is variety of thicknesses & colours, other sizes and can be purchased as a specific size or a full roll. Custom sizing is also available on request.
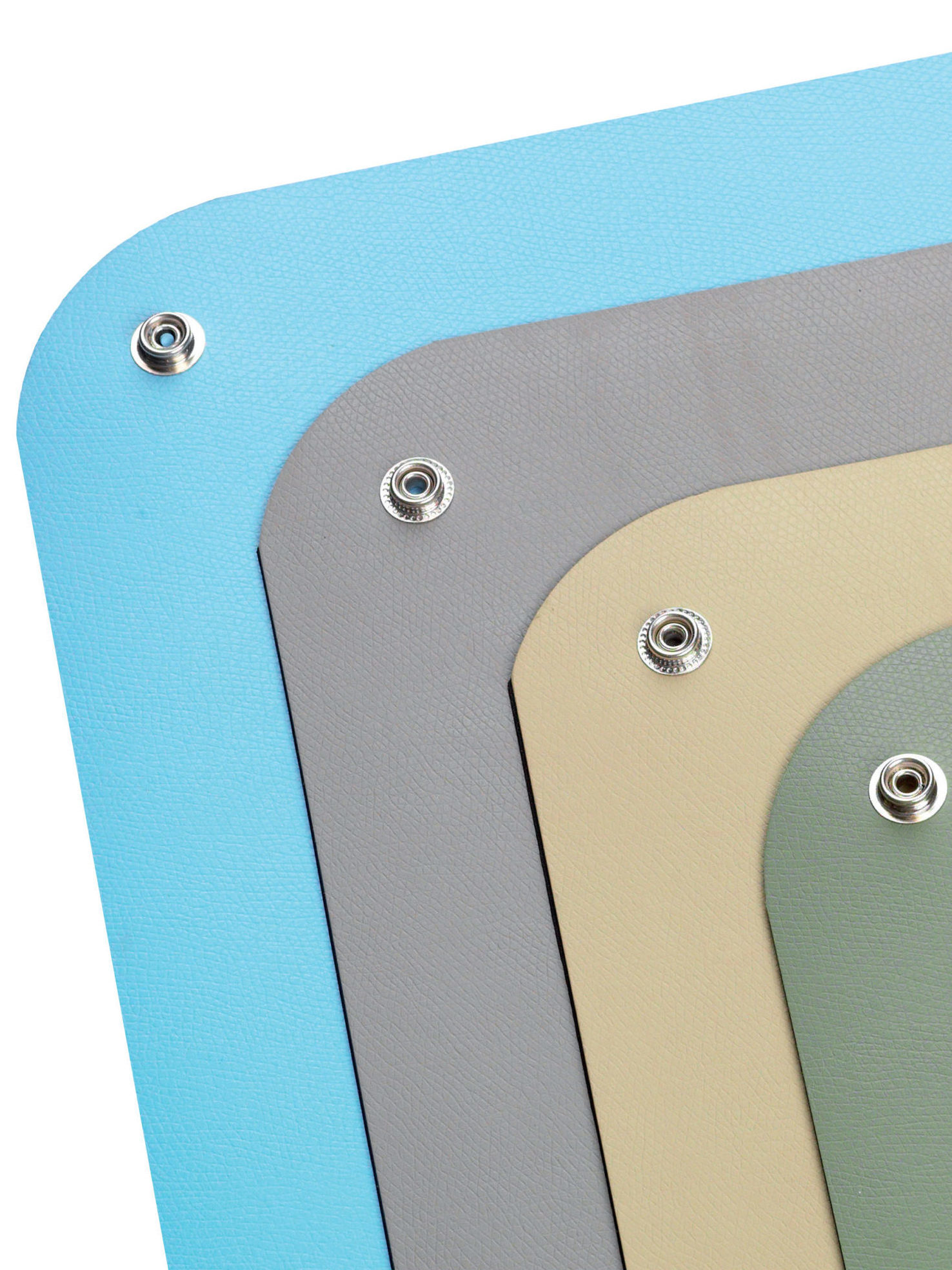
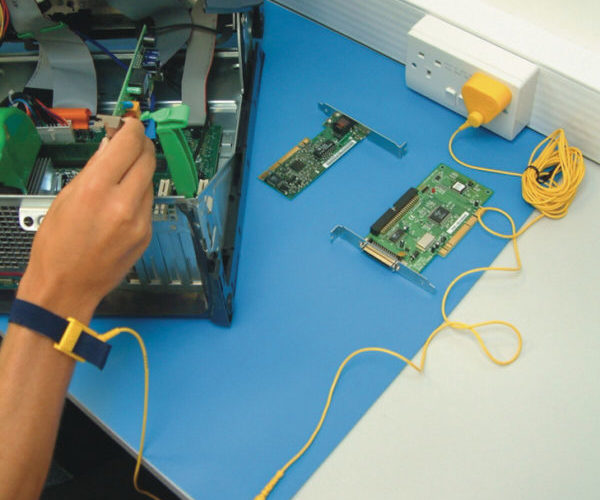
How Do ESD Mats Function?
Antistatic mats help to protect static sensitive components from electrostatic discharge. They are engineered to drain static discharge from items placed on their surface. They also serve to protect the surface of the ESD sensitive devices from wear and tear by slowing down the flow of static charge, and moving the charge into the grounded mat, away from the components. The performance of ESD matting is based on the material it’s constructed with, as well as its electrical properties and ability to withstand heat, chemicals and mechanical abrasion.
Types of ESD Mats
Bench Mats – Usually available in either smooth or lightly embossed finishes. Embossed finishes are recommended as they help to reduce the surface’s reflective properties, reducing glare and improving operator comfort. Bench matting is generally supplied in bright, light colours to help workers find smaller components on their surface, and are designed to be used with other ESD controls such as wrist straps and grounding points.
Floor Mats – Floor mats are larger and thicker than table mats due to their durability requirements and feature heavier embossing, to prevent workers from slipping. Many come with anti-fatigue cushioning to improve operator comfort during long periods of standing and are typically supplied in dark colours to hide dirt and scuffs. When using ESD floor mats, ESD footwear should also be worn to allow full grounding and earthing.
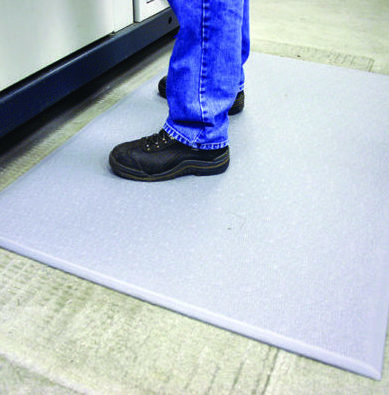
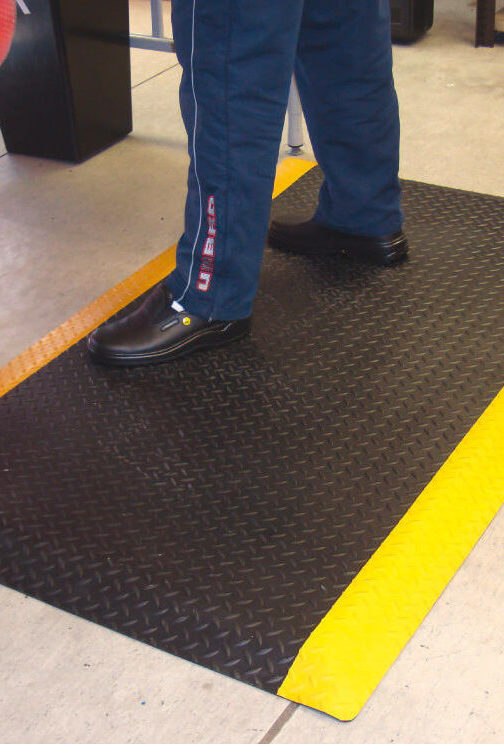
ESD Mats Composition
Before choosing your matting, there are four ESD matting compositions you should consider:
Homogenous (Vinyl and Rubber) – Made of a single layer polymer mix and therefore consist of the same material throughout. These mats provide good mechanical service with electrical performance normally limited to about 109 to 1010 RTG.
Three Layer (Vinyl) – Constructed from a conductive metal/carbon layer between a top surface of the vinyl and a layer of vinyl on the back. The conductive layer improves the electrical properties by acting as a fast track to move the static charge to ground. The foam back layer provides a cushioning effect, making it easier to pick up parts.
Two Layer (Vinyl) – Combines the foam from the three-layer mat and the dissipative vinyl from solid mats. A cost effective option, however as it contains no metallised layer it provides average electrical performance.
Two Layer (Rubber) – This option provides a top layer of static dissipative rubber and the back layer of conductive rubber, giving the same electrical performance as the vinyl three-layer mat, but with great tolerance to heat and chemicals.
Vinyl v Rubber Matting
Vinyl Mat Advantages:
- Generally, vinyl mats are most widely used for table top or work surface applications.
- Vinyl mats are cost-effective, easy to cut to shape and provide excellent static dissipation.
- Vinyl floor matting is suitable to use for electronics manufacturing applications that require the use of ESD footwear.
Rubber Mat Advantages:
- Heat resistant (resistant of hot solder; whereas Vinyl material will melt). Ideal for use where high resistance to heat and chemicals is required.
- Remain in its same form, whereas vinyl mats can change and become harder in cold conditions.
- Identified as more environmentally friendly that Vinyl options
- Rubber mats are stable; ESD properties cannot change.
- More cost effective than Vinyl options
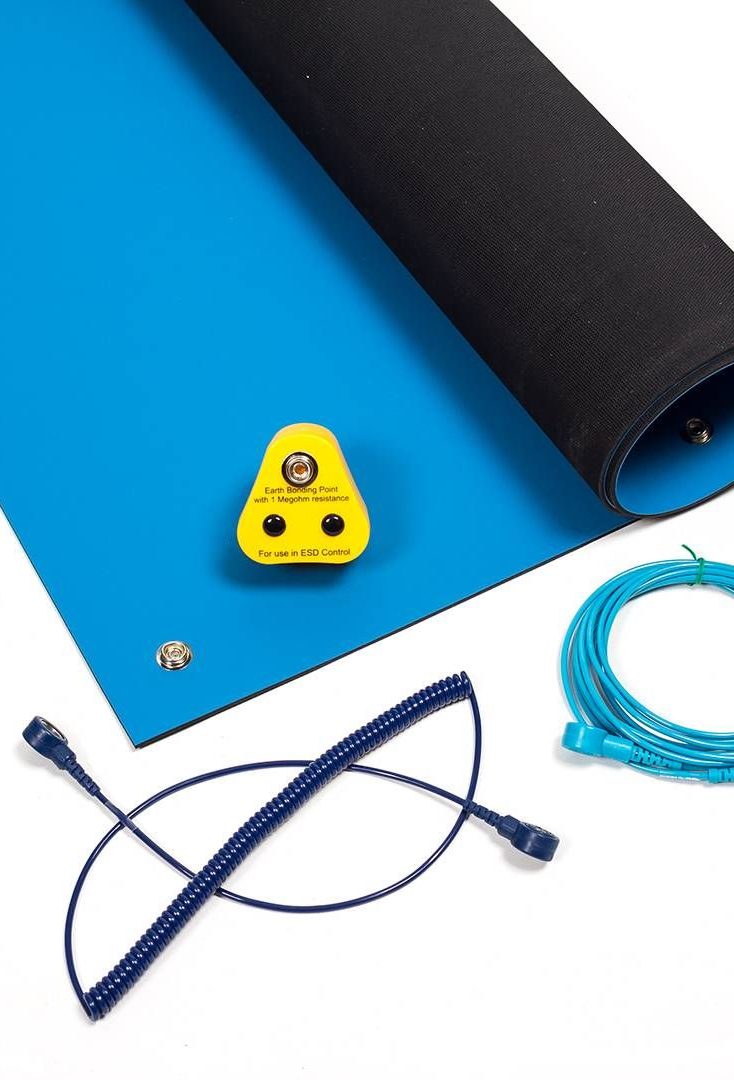